Energy Control
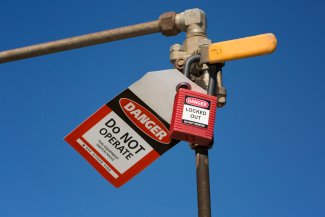
Price
Purchase
Overview
For most workers in the process and energy industries the biggest hazard that they face is the possibility of injury or death from a source of high energy such as pressure, temperature, toxic chemicals, electricity, moving parts, pneumatic and hydraulic equipment, or falls from heights, often due to failure of the lockout tagout system. Therefore, before working on a piece of equipment, particularly before it is opened for inspection or maintenance, the associated sources of high energy must be identified and either removed or isolated from the workers.
This ebook outlines a six-step process for organizing and implementing an Energy Control program. Additional topics covered include minimizing contact with air, equipment isolation, lockout / tagout, work permits, confined space entry, hot tapping and the clearing of plugged lines.
The third means of protecting maintenance workers is to use lockout / tagout. (It is often used in conjunction with other isolation methods). Once a switch or valve is in the correct position it is locked so that it cannot be moved, and a “Do Not Operate” tag is attached to it. (Valves are often chained in place, with the lock being used to secure the chain such that the valve handle cannot be moved.)
In spite of the security that a lockout system provides, it is less safe than the use of positive isolation methods. First a valve may leak while it is in the closed position. Second, in spite of all precautions, someone may remove the lock before the work has been finished. There is also a chance of confusion; the wrong valve may be chained closed, while the valve that should have been secured is left in its normal operating state.
Table of Contents
Introduction
Regulations and Standards
29 CFR 1910.119
API 2015
API 2026
API 2217A
ANSI Z117.1
NFPA 69
Example
Risk Management
Energy Control Program
Step 1 — Job Hazards Analysis
Step 2 — Work Permit
General Work Permits
Hot Work Permits
Confined Space Permits
Issuing the Permit
Multiple Work Permits
Changes in Conditions
Barrier Tape
Step 3 — Vent, Drain and Purge
Inert Gas
Air-Blowing Hydrocarbon Lines
Step 4 — Isolate the Equipment
Positive Isolation
Level 1 — Closed Valve
Level 2 — Closed Valve with Open Bleeder
Level 3 — Double Block and Bleed
Level 4 — Block and Bleed with Line Break
Level 5 — Block, Bleed and Spectacle Blind
Level 6 — Double Block and Bleed with Blind
Level 7 — Double Block and Bleed with Line Break
Non-Positive Isolation
Administrative Controls
Pipe Plugs
Step 5 ─ Open the Equipment
Test for Oxygen
Heavy Sludge Deposits
Step 6 — Complete Work / Return to Service
Lockout / Tagout
Car Seals
Group Lockout / Lockboxes
Padlocks
Tags
Removing Locks and Tags
Electrical Isolation
Confined Space Entry
Types of Space
The Entry Permit
Personnel
Entrant
Supervisor
Manway Attendant
Gas Tester
Rescue Team
Test
Excavations
Preparations
Inspection
Cave-In Protection
Tie-Ins
Hot Tapping
Plugged Lines
Prevention of Pluggage
Unplugging a Line
Mechanical
Differential Pressure
Fluid Selection
Steam
Compressed Gas
Copyright © Ian Sutton. 2024. All Rights Reserved.