Hyperloop Generic Safety Study
In Safety Moment #8: “But We’re Different, You Know” we show that risk analysis techniques have much in common across different parts of the process and energy industries. Lessons can be shared across industries such as oil refining, chemicals manufacture, pipeline operations and offshore oil and gas production. But, given that the first word in the phrase Process Safety Management (PSM) is process it might be thought that the principles of PSM cannot be used in totally different types of industry that has nothing to do with chemical or energy processing. Yet this conclusion is incorrect. The management of risk in large industrial systems has much in common, regardless of the technology being considered. An example is to do with the new transportation system known as hyperloop.
It is way outside the scope of this very brief Safety Moment to describe the technology behind hyperloop — particularly as it is still in development. Briefly, hyperloop is a transportation system in which pods travel through low pressure tubes at high speed. The pods are magnetically levitated above the floor of the tubes, so there are no wheels or tracks. And they are driven by linear induction motors. There is a narrow gap between the pods and the internal wall of the tube.
Although there are many technical issues to be resolved, and different organizations are proposing different basic designs, it is nevertheless not too early to start developing a generic safety study or safety case for this new technology. An analogous situation occurred in the year 1975 with the publication of the Reactor Safety Study — often referred to by it index title: WASH 1400. That report — which certainly had its limitations, as became apparent following the Three Mile Island incident — was nevertheless instrumental in introducing risk management techniques such as Probabilistic Risk Analysis.

An analysis of a generic hyperloop system could follow the normal process safety approach consisting of the following steps:
- What could wrong — what are the hazards?
- What are the consequences of those hazards with respect to both safety and operability?
- What is the likelihood of those hazards occurring?
- What are the safeguards that would reduce consequences and/or likelihood?
Hazards
The first step in any risk analysis is to define the hazards, i.e., to determine what could go wrong. Two particular hazards with regard to hyperloop operations are:
- Total power failure; and
- Large leak of air into the tube.
Power Failure
Hyperloop transportation is totally reliant on electrical power to move the pods forward, to keep the pods elevated above the “track”, and to remove air from the tubes. Therefore loss of power would cause the system to stop working. And, given that the pods are traveling at high speeds, could create a safety issue as they come to a stop.
Large Air Leak
Were there to be large rupture of the tube, such as would be caused by it being hit by a vehicle, air could enter the tube faster than the vacuum pumps could remove it, so the pressure in the tube would risk very quickly. This would certainly cause the pods to come to a stop. But it may also create a situation where they lose directional stability and crash into the inside wall of the tube.
Consequence Analysis
Having identified the hazards, the next step is to determine the consequences (safety, environmental and economic) were the hazard to occur. Using Fault Tree terminology (a technique that is at the heart of WASH 1400), IF there were to be an electrical power failure AND IF the safeguards such as battery backups were to fail, THEN the consequences could be catastrophic. As already mentioned, the pod could veer to one side and crash into the tube wall while traveling at very high speed. (This is not a problem with airplanes because, in an emergency, they have room to move around the sky without hitting anything.) A large air leak could have similar consequences, except that it would be harder to come up with safeguards.
Frequency Estimation
Having identified the hazards and their consequences, the next step is to estimate the frequency with which these events may occur. This can be done using historical data and with techniques such as Event Tree analysis.
Safeguards
Finally, consideration can be given to safeguards. These might include:
- Landing wheels on the pods that would “touch down” on some type of track.
- Emergency compressors ensure that the air pressure does not fall too quickly.
- Reinforcement of the tube to minimize the chance of a large leak.
Risk
Total risk can be obtained by calculating the risk value for each hazard, and then adding all the individual risk values together — usually in terms of fatalities per thousand years. The result of this exercise is sometimes plotted in the form of an FN curve as shown below, in which the ordinate represents the cumulative frequency (F) of fatalities or other serious events, and the abscissa represents the consequence term (usually expressed as N fatalities).
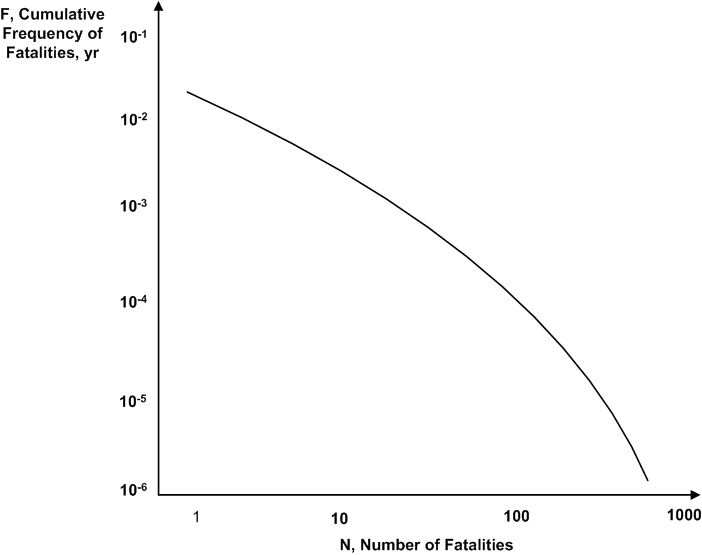
Conclusion
The above discussion, although extremely limited in scope, does show how the principles of process safety management can help evaluate the risk to do with brand new technology in a technology that is profoundly different from the process and energy industries. The manner in which risk is evaluated is the same, regardless of the industry.
You are welcome to use this Safety Moment in your workplace. But please read Use of Safety Moments.
Copyright © Ian Sutton. 2020. All Rights Reserved.