Frequency Analysis
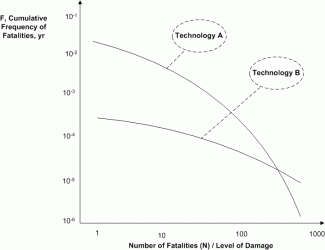
Price
Purchase
Frequency Analysis
This material in this ebook describes risk quantification. It shows how to estimate how often incidents may occur. Topics covered include risk ranking, fault tree and event tree analysis, Monte Carlo simulations, Markov models, safeguards and Layer of Protection Analysis (LOPA). Also discussed are the sources and management of failure rate data.
The quotations, “What gets measured gets done” and “You become what you measure” are well known. This means that, if risk is to be properly understood and reduced to an acceptable level then quantification is needed.
The basic risk equation is:
RiskHazard = Consequence * Predicted Frequency............. (17.1)
This ebook discusses how a value for the Predicted Frequency term can be obtained (the distinctions between frequency, predicted frequency, probability and likelihood are explained in Chapter 1 of Process Risk and Reliability Management. Concepts covered include:
- The Pareto Principle: identifying the important few and ignoring the unimportant many;
- Fault trees;
- Event trees;
- Monte Carlo simulation;
- Markov models; and
- Layers of Protection Analysis.
The Pareto Principle
In the late nineteenth century the Italian economist and misanthrope Vilfredo Pareto (1848 – 1923) famously noted that most of the wealth in a community was held by a small proportion of the population. From this insight he developed the 80/20 rule, or the Pareto Principle, which, in the case of community wealth, meant that about 20% of any population owns about 80% of the wealth.
His principle, which has no theoretical underpinning, is widely observed to be true in many fields of human activity (Juran 1951). It is applied here to the topic of risk analysis in the process industries.
The Pareto Principle can be expressed mathematically.
log n = c + (m * log x).................................................... (2)
where n is the number of items whose value is greater than x; c and m are constants.
Examples of the principle’s applications in an industrial context include:
- 80% of a company’s sales come from 20% of its customers.
- 80% of a company’s sales are made by 20% of the sales force.
- 20% of the workers are involved in 80% of the accidents.
- 20% of the equipment items cause 80% of the facility shutdowns.
- 20% of a company’s products will account for 80% of the total product defects.
- 80% of weight loss during a diet is achieved with the first 20% of the effort.
In each of the above examples, an ‘important few’ or the ‘vital few’ have a great impact on the business, whereas the ‘unimportant many’ are much less significant. Therefore a safety manager should direct his or her program toward that minority of incident-creating workers. Spending time on the ‘unimportant many’ is not likely to have much benefit.
One commonly-held misconception to do with the Pareto Principle is that 80% of the problems can be resolved with 20% of the resources. In fact the Principle makes no statement at all as to how much effort is needed to address the contributing factors.
Table of Contents
Introduction
The Pareto Principle
Importance Ranking
Fault Tree Analysis
Gates
OR Gate
AND Gate
VOTING Gate
Events
Top Event
Intermediate Events
Base Events
House Event
Top-Down Development of a Fault Tree
1. Define the Top Event
2. Build the Tree
3. Identify the Cut Sets
4. Eliminate Repeat Sets
5. Eliminate Repeat Events in a Set
6. Eliminate Redundant Events
7. Quantify the Risk
Mathematics of an OR Gate
Mathematics of an AND Gate
Mathematics of a Voting Gate
Cut Set Quantification
8. Risk Rank
Event Contribution
Important Few
Unimportant Many
Power of the AND Gate
Importance Equalization
Cost-Benefit Analysis
Importance Ranking Using Cut Sets
Birnbaum Factor Method
Fussell-Vesely Method
Perturbation Method
Common Cause Events
Fukushima-Daiichi
Generic Fault Trees
Generic Safety Fault Tree
Generic Reliability Fault Tree
Discussion of the Fault Tree Method
Qualitative Fault Tree Analysis
Event Tree Analysis
Quantification of an Event Tree
Scope of Event
Combining Event Trees and Fault Trees
Short Sequence of Events
Many Events
Partial Success
Discrete Event Analysis
Non-Linearities and Complexities
Conveying Statistical Uncertainty
Monte Carlo Simulation
Random Number Generators
Seed Numbers
Speeding the Simulation
Markov Models
Top-Down / Bottom-Up Approach
Top-Down
Bottom-Up
Qualitative Insights
Limitations to Quantification
Mathematical Understanding
Value-Laden Assumptions
Lack of Exhaustivity
Human Behavior
Data Quality
Safeguards
Safeguard Level 1: Normal Operations
Safeguard Level 2: Procedural Safeguards
Safeguard Level 3: Safety Instrumented Systems
Safeguard Level 4: Mechanical Safeguards
Safeguard Level 5: Passive Safeguards
Safeguard Level 6: Emergency Response
Layer of Protection Analysis
The LOPA Process
Single Scenarios
IPLs
Specific
Independent
Dependable
Auditable
Human Response
Implementing LOPA
Team Makeup
Timing
Tools
Procedures and Inspections
Risk Criteria
Failure Rate Data
Conditional Probability / Bayes’ Theorem
Evaluation of Tests
Sequential Observations
Combining Data Sources
