Safety Moment #64: Equipment Spacing (Hydrocarbon Storage Tanks)
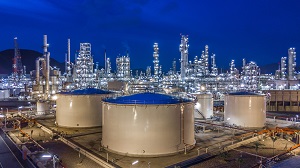
Safety Moment #57: Equipment Spacing (Pumps/Fireproofed Pipe Racks) described the layout of pumps in a process or energy facility. Continuing the discussion, this Safety Moment describes some of the issues to be considered with regard to the layout of storage tanks, sometimes referred to as “API Tanks”. (The design and operation of storage tanks is discussed in Safety Moment #73: Storage Tanks in the Process and Energy Industries.)
With regard to the layout of tanks the following general guidance is provided.
- Tanks should be located at a lower elevation than process areas so that if one of the tanks leaks and the secondary containment is not effective, flammable and toxic materials will not flow into the process areas. (The same argument holds if the spilled liquid could create a vapor that is denser than air and that could then flow downhill).
- For the same reason tanks should not be located above populated areas.
- Where it is not feasible to locate tank farms at elevations lower than process areas, increased protection measures may be required to offset the increased potential for ignition. These measures may include:
- Diversion diking
- High-capacity drainage systems
- Vapor detection placed near potential release points
- Increased fire protection
- Spacing between tanks should be great enough to contain a fire, prevent spread of the fire to other tanks, and to allow sufficient access for firefighting crews.
- Equipment other than associated piping should not be located within the diked area of storage vessels.
- Flammable gas detection is not usually required for open tank areas unless a potential for gas accumulation has been identified.
- Toxic gas detection should be installed if the potential exists for gas accumulation in a tank area. Alternatively, entry into a bermed area must be treated as a confined space entry.
- Fire detectors should be provided for tanks containing combustible or flammable liquids.
Secondary containment is frequently installed around tanks and tank farms. It generally consists of a containment or bund wall around equipment or tanks containing large volumes of liquid. If the equipment leaks or the tank is over-filled the liquid is contained and thus prevented from flowing into other parts of the facility, where it could create a safety and environmental problem.
Such a system, which is illustrated in Figure 2.3, which is taken from the book Plant Design and Operations, is totally passive and therefore inherently safe. It requires neither instrumentation nor human intervention to be effective.
Figure 2.3
Secondary Containment

The general rule is that the secondary containment should have a volume equal or greater to 110% of the volume of the largest tank being protected. If multiple tanks are enclosed, then only a spill from one tank need be considered.
Although a system such as that shown in Figure 2.3 is inherently safe, the drain valve in the wall has to be checked. It is needed because in order to drain accumulated rainwater from the contained area. But, if the valve is left open or if the drain line is broken, say by a passing vehicle or by someone treading on it, then any tank leak will bypass the secondary containment.
The material in this safety moment is taken from the book Plant Design and Operations and from the ebook Siting and Layout.
You are welcome to use this Safety Moment in your workplace. But please read Use of Safety Moments.
Copyright © Ian Sutton. 2020. All Rights Reserved.