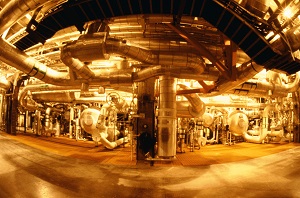
This topic covers the design of piping and valves, and their role within a process safety management program. Discussions to do with equipment are provided at this topic page.
The following is a list of the typical piping and valves that are covered by an asset integrity program.
- Pipe (specifications and sizing)
- Materials
- Equipment
- Piping
- Fittings
- Flanges
- Gaskets
- Blinds
- Flame Arrestors
- Vortex Breakers
- Hoses
- Block Valves
- Globe / Control Valves
- Rotary Valves
- Check (Non-Return) Valves
- Flangeless Valves
- Valve Seat Materials
- Valve Position
- Steam Traps
- Pressure Safety Relief Valves
- Thermal Relief Valves
- Rupture Disks
Articles, safety moments and other publications to do with piping and valves are shown below.
Copyright © Ian Sutton. 2018. All Rights Reserved.
Safety Moment #75: Pressure Tests
After a piece of equipment or piping that operates under pressure has been opened and then reassembled (buttoned up) it must be pressure tested before being put back into service.
Safety Moment #76: Plugged Process Piping
Process lines, piping and valves frequently become plugged. If line pluggage is a recurring problem it is best to try and identify ways in which the problem can be prevented from occurring. If that solution is not possible then valves, drains, tees and connections should be designed so that it is possible to remove the pluggage safely and with minimum time and expense.