Safety Moment #89: Layout of Process Facilities
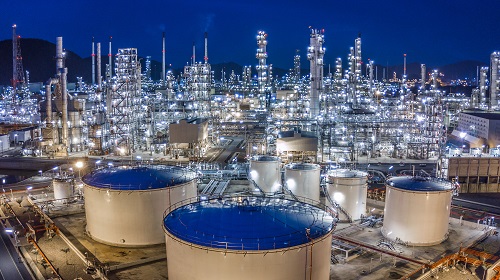
Siting / Layout
The words ‘siting’ and ‘layout’ are often used interchangeably, but, strictly speaking, they have different meanings. Siting is concerned with the location of a facility. For example, if a company is planning on building a new chemical plant its management may consider the relative merits of sites in Texas, Mexico or China.